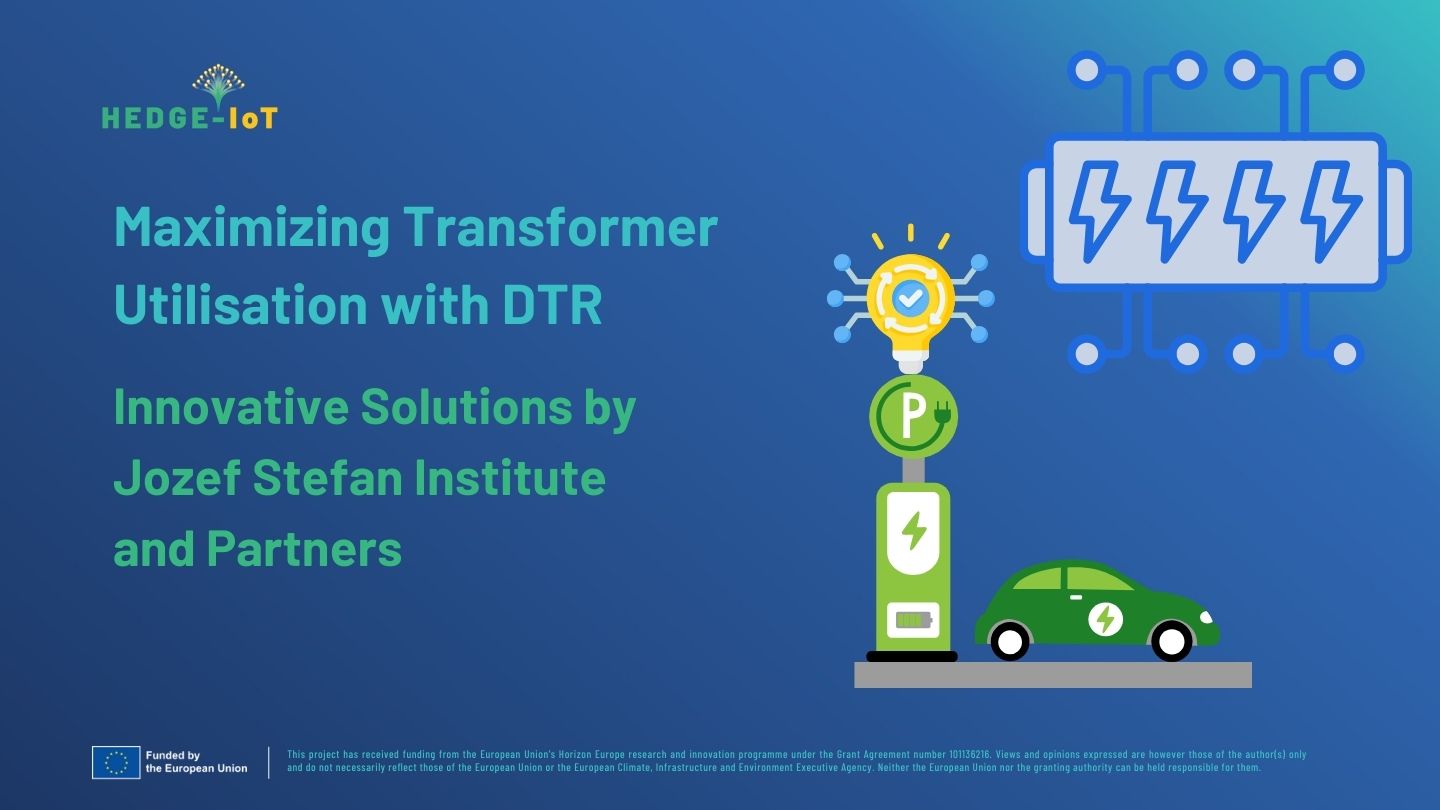
The low-voltage distribution grid is facing a rapid peak load growth, mainly due to the massive transition to electric heating and the increasing integration of electric vehicle charging infrastructure. The pace of emerging problems, given the massive integration of renewables, drives the development and utilisation of Dynamic Thermal Rating (DTR) technology to gain an extra load band while leaving operational safety intact. DTR is a system operation concept aiming at maximizing utilization of the equipment (power lines, transformers) when weather conditions allow it, without compromising the safety of operation and without a negative impact on the life expectancy of the equipment.
Power transformers are designed to operate throughout their lifetime at pre-defined ambient conditions in line with international standard requirements. At 40 °C ambient temperature and nominal loading, a typical actual transformer’s loading capability, or shorter – loadability, can be considered a static value, as defined on the naming plate. If the transformer is cooled down due to cooler ambient conditions (e.g., during colder seasonal periods) or during periods when loading is below the nominal, transformer operation above rated power is possible without exceeding the specified temperature limits and without compromising the transformer’s operational reliability and normal life expectancy.
Together with Operato, Elektro Gorenjska and the Milan Vidmar Electrical Institute, we carried out a TrafoFlex project with ambition to deploy an operational DTR system in the Slovenian grid. Our task was to develop a physical model that adequately describes the thermal state of the transformer, implement its numerical solution and deploy the model in operation. Conventional models described in standards and their further developments attempt to capture the entirety of the non-linear heat transfer dynamics with a single exponent parameter. This is a reasonable approach for modelling a wide spectrum of transformers with the simplest applicable model and a set of given parameters. Nevertheless, our ambition to simulate different types of transformer enclosures with generalised parameters forced us to take a more granular approach and considered each physical mechanism of heat transfer separately. We constructed a generalised multi-mass model that allows us to simulate the heat transfer between N sequential bodies using different mechanisms of heat generation/transfer. We have opted for the model with two inner mass bodies for the transformer and one outer mass body for the enclosure. The latter is not considered in the simulation of pole-mounted transformers.
Due to weather data availability limitations, we only use the modelled terms that rely on measured temperature. The ambient temperature is measured outside the transformer enclosure and used as input for our model. The error between the modelled and measured top liquid and internal enclosure temperatures are minimised with Powell minimization method. Due to the high number of parameters and the model’s nonlinearity the problem has many local minima. This problem is resolved by using a stochastic approach to minimization where we use the known relations between physical characteristics and parameter values to determine reasonable boundary values that we used to randomly generate initial values for the optimization method.
Within the scope of HEDGE-IOT project we will implement the model in a substation on an embedded system that will be supplied observations from a local weather station. For the purposes of DTR forecast, we will implement a local short-term forecast based on weather measurements by using statistical methods.